Author |
Topic: Newest McGregor Build Completed! LA LUNA |
Don McGregor
From: Memphis, Tennessee
|
Posted 19 Oct 2014 3:50 pm
|
|
Announcing the long awaited completion of LA LUNA, steel of my dreams. Finally.
She has Lacewood necks and rails, and an African Mahogany, stair stepped deck.
These amazing, clear, acrylic, Lunar Phase fret boards, that allow the full grain of the Lacewood to show through were designed, laser etched, and polished by my good friend Mark Bracewell, Chief Luthier and Magician at Willow Glen Guitars. Mark is also a very fine fellow. The finish is a light Amber Aniline dye sealed with a couple of coats of shellac, several coats of pore filler, and many coats of nitrocellulose lacquer applied with rattle cans, and level sanded between every four coats.
Not finding a source for new end plates or aluminum key heads, I have re-purposed these, which I purchased used, cutting down two sets of 10 string key heads into 8 stringers.
I routed the pickup cavities to fit either George L’s, which, so far, I am liking a lot, or narrow mount Jerry Wallace Truetones, which I already know I like, and which I also have on hand. I will be changing the pickups back and forth until I settle on one. I feel certain other pickups would fit, also.
Thank you to everyone on this forum for providing me and the rest of the entire steel guitar community with advice, information, and caring. Of course, I owe the biggest thanks of all to my wife and children for putting up with me spending so many hours out puttering around in the shop while the world goes on whirling around outside.
 |
|
|
 |
Jon Light
From: Saugerties, NY
|
Posted 19 Oct 2014 3:56 pm
|
|
Congratulations! What a beautiful guitar. You deserve to feel proud. |
|
|
 |
Ken Campbell
From: Ferndale, Montana
|
Posted 19 Oct 2014 4:07 pm
|
|
Goodness yes. Spectacular! |
|
|
 |
Tom Pettingill
From: California, USA (deceased)
|
|
|
 |
Paul Honeycutt
From: Colorado, USA
|
Posted 19 Oct 2014 4:29 pm
|
|
Amazing! That's such a beautiful guitar. Post some sound clips when you can. |
|
|
 |
Bill Hatcher
From: Atlanta Ga. USA
|
Posted 19 Oct 2014 6:52 pm
|
|
nice!!!! congrats!!! |
|
|
 |
Mike Neer
From: NJ
|
Posted 20 Oct 2014 3:48 am
|
|
I admire your building skills, Don. Best of luck with that beauty! _________________ Links to streaming music, websites, YouTube: Links |
|
|
 |
Peter Jacobs
From: Northern Virginia
|
|
|
 |
norm mcdaniel
From: waco tx
|
Posted 20 Oct 2014 6:14 am
|
|
Don---I wish Oh how I wish I had one as well. Verry nice guitar and all parts too
Best of Luck
Norm in Waco Tx  |
|
|
 |
Don McGregor
From: Memphis, Tennessee
|
Posted 21 Oct 2014 11:29 am
|
|
Building an instrument is a learning experience, and this one taught me a lot. I now know where I want to go with my next couple of builds.
Thank you all again for all your positive support.
I will try to get a recording up soon. |
|
|
 |
George Piburn
From: The Land of Enchantment New Mexico
|
Posted 21 Oct 2014 2:43 pm Beautiful
|
|
Congratulations Don - looks great !!
We have learned to take the Brass to a plate shop for Buffing and Nickel plating.
It eliminates the eventual Tarnish that Brass gets, only need to wipe to shine up during string changes.
The Nickel plate preserves the quality tone of the Brass - Chrome is too hard and alters the tone to a more Sharp Quality.
I am a big lover of LaceWood -- you have a collectible in your estate now.
Looking Forward to more of your awesome builds.
GeorgeBoards |
|
|
 |
Don McGregor
From: Memphis, Tennessee
|
Posted 21 Oct 2014 6:37 pm
|
|
Thank you, George. I do like the look of tarnished brass, myself, but also love Nickel. I am planning on having some plating done in the future. I may even pull these parts off at some point, and get them plated. I have a few Nickel plated bridges set aside for the next few builds. This only my second build, so I am trying different things. One thing I discovered is that Lacewood is a VERY porous wood, and takes a LOT of grain filling. My hat is off to anyone who gets a perfect, mirror, Lacquer finish on it. It took me a while to get a handle on it. |
|
|
 |
Ron Mielzynski
From: Illinois, USA
|
Posted 22 Oct 2014 5:57 am
|
|
Beautiful piece. Lots of nice details in those close up pics. _________________ RAM Guitars
www.RAMguitars.com |
|
|
 |
Tom Pettingill
From: California, USA (deceased)
|
|
|
 |
George Piburn
From: The Land of Enchantment New Mexico
|
Posted 22 Oct 2014 11:33 am YES ZPoxy
|
|
We use the ZPoxy , and get it from Amazon typically from a hobby shop. I get the 15 minute Finishing.
It has a light amber to it , and will darken your project a tiny bit , but it is desirable.
Another Tip is to Thin it some with Denatured Alcohol which help to drive it down into the grain.
You may need to do the treatment 2-3 times but not to worry, the clear lacquer will instantly make any funky looking stuff go clear.
We use a Blade from a Utility knife and old tee shirt doused with the Denatured to wipe after each scrape. You do the scrape while the ZPoxy is gelling up, to make it go easier, and reduce sanding after the treatments.
Make certain you allow it to dry 24 hours before each re-treatment, and to dry scrape it as well.
All of this will make the lacquer later go so much easier and way less coats to get to the mirror status.
Thank you Tom for bringing this up!
 |
|
|
 |
Don McGregor
From: Memphis, Tennessee
|
Posted 22 Oct 2014 2:37 pm
|
|
WOW, Tom and George. I googled until my fingers were numb looking for something like this. I will definitely use it next time. I did find, and wind up using a product called "CrystaLac", which worked pretty well, though at times it seemed a little too thick for some of the pores. It took several applications, and still many coats of lacquer to finally get something I could really buff out.
I look at the Pettingill and Georgeboards posts all the time, and then go out in the shop, and try to figure out how I can do that. I am continually in awe of the beautiful instruments you guys turn out. It means a lot to receive encouragement from builders like you. |
|
|
 |
George Piburn
From: The Land of Enchantment New Mexico
|
|
|
 |
Don McGregor
From: Memphis, Tennessee
|
Posted 22 Oct 2014 5:36 pm
|
|
I just ordered mine, too. Thank you both for the great tip. |
|
|
 |
Tom Pettingill
From: California, USA (deceased)
|
Posted 23 Oct 2014 10:04 am
|
|
Always glad to help if I can
A quick tip. Zpoxy flows, spreads, and levels very well, but as we get into winter months, colder weather will make it thicker. After I get it all squeegeed off, I'll hit it with a hair dryer and warm things up. It helps to let the resin sink into the pores and lets air bubbles to come to the top.
In all, I think that you will like the Zpoxy, but no matter how you cut it, grain filling has been the bane of fine finishers for generations.
On finishing in general, there is no quick and easy, just different levels of not so bad. Most don't realize, but you can get some serious time invested in an instruments finish. The most important part of the whole process is patience. In the end, you will forget all about the pain when its done.
.
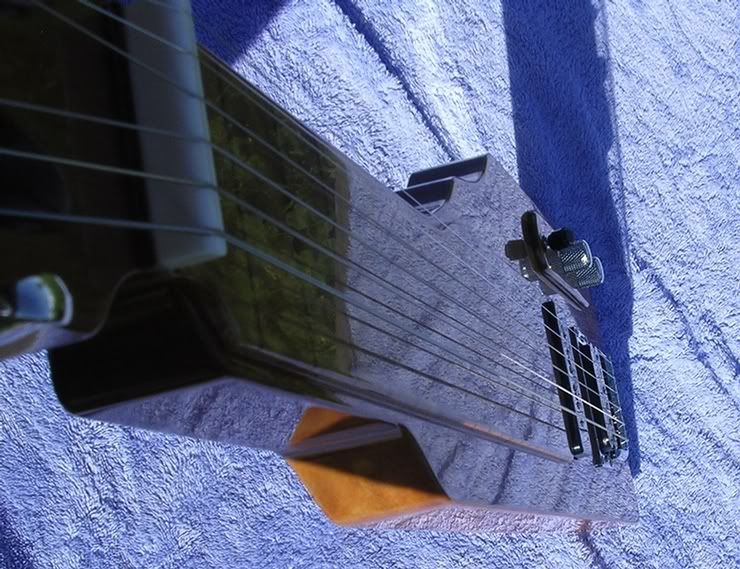 _________________ Some misc pics of my hand crafted steels
Follow me on Facebook here |
|
|
 |
Don McGregor
From: Memphis, Tennessee
|
Posted 23 Oct 2014 6:30 pm
|
|
My shop is not insulated yet, so Winter is a hard time to find conditions conducive to fine finishes. Too, I'm in the soggy Delta, so I have to wait for the humidity to drop down and play nice. Sounds like I will be using a hair dryer soon. That picture is what I'm shooting for. |
|
|
 |