Author |
Topic: Lap steel construction, contribution to tone. |
John RJ Wilson
From: United Kingdom
|
Posted 27 Aug 2013 2:45 am
|
|
Talking here about 6 string electric lapsteel. I have seen electic lap steels made to all types of design from mini Les Pauls to being made out of skate boards. Planks of wood with hardware attached etc. Beautiful hand made instruments. Composite, stainless steel, wood, plastic. Does the body/neck have any real bearing on the tone, or does it carryout a merely an aesthetic function and base for the pickup, nut, bridge etc. The fret board is not actually fretted etc etc. Is the tone from a lap steel inherently buried in the ability of the player, more than any other stringed instrument, and is construction secondary. Obviously a steel made out of 1/4 inch carboard is going to lack something, but where does the tone involvement end and pure aesthetics kick in. Obviously the scale length, pickups etc will have a bearing on tone. Or put it more simply. A precisely built lap steel made out of 6 inch by 2 inch redwood, with quality hardware and precise build, will sound better or worse than the same design made out of mahogany with a laminated maple cap?? I am assuming craftmanship in the build, not an instrument thrown together here, as inprecise measurement etc will obviously have an adverse effect. I am not in any way trying to suggest that there is no way there is any point in buying a custom built lap steel from a master luthier/builder, I am asking from a technical point of view. I clearly would not ask this question of a violin maker.
Sorry about the length of this post.
J  _________________ Guyatone HG-91, Fender Hot Rod Deluxe, Ernie Ball Jr volume pedal. |
|
|
 |
Stephen Abruzzo
From: Philly, PA
|
Posted 27 Aug 2013 4:21 am
|
|
Body wood can have an impact on the sound of the pickups by either "darkening" or "brightening" the overall tone produced. Body wood can also impact sustain, etc.
So, in theory, you want to maximize the positives and minimize the negatives.....in other words, you don't want the body wood working "against" the pickups.
Depending on your builder, he/she may ask how you want the lap steel to sound, what type of music you primarily intend to play, etc......and then make recommendations on pick-ups and body wood.
Finally, the quality of the wood itself is an issue....as in do you want your steel (or any guitar for that matter) made from any old piece of mahogany, or from a choice cut? Which could be a reason as why the exact same model of a guitar with the same pickups will sometimes sound "different" than another.
My steels were made from premium cuts of curly maple (humbuckers), mahogany (SC and P90), and swamp ash that was chambered with a black walnut cap (SCs). |
|
|
 |
Tom Pettingill
From: California, USA (deceased)
|
Posted 27 Aug 2013 9:34 am
|
|
Quote: |
... in theory, you want to maximize the positives and minimize the negatives ... |
Steve hit on some great points and the above quote really hits on an important part of building any instrument.
Take for example your extreme theoretical cardboard steel. Its easy to identify the negatives on the extreme, but think of how what makes 1/4" cardboard a bad idea relates to real world instrument construction, like a headstock for example. Even in hardwood, a thin headstock will flex more than a thicker one. If that headtock is flexing, then your losing potential sustain. Its a good example of balancing the pros and cons. That is one reason I make my typical headstocks 5/8" instead of the more common 1/2" thick. An 1/8" might not sound like much to worry about, but beyond adding more rigidity, the shorter tuner post sticking out the top means you get a little better break angle over the nut too. Its a small detail, but its a win win. Its minimizing the negatives and maximizing the positives.
Quote: |
Or put it more simply. A precisely built lap steel made out of 6 inch by 2 inch redwood, with quality hardware and precise build, will sound better or worse than the same design made out of mahogany with a laminated maple cap?? |
I would not say better or worse, just different. I've not built a redwood steel for comparison, but with mahogany compared to maple capped mahogany, the maple adds a bit more snap and brightness. The amount it adds is dependent on the thickness of the cap. And to add to the complexity of the equation, what species of maple? Hard rock eastern sugar maple? Western big leaf? And then what kind of mahogany? To further muddy the waters, there are subtle differences even within the same species and even the same tree.
As to material and construction in general, My take on the subject is that an instruments voice is the sum of its parts and construction. The pickup(s) and electronics contribute the lions share to the base tone, but the rest of it, like woods, bridge material, etc contribute too, much like the spices in a dish. I mean, I like a little salt on frys, but there is such a thing as too much.
And I don't buy into the whole "tonewood" only hype where there are only certain species you can use. Though, I do buy into select woods suitable for making great instruments. And it does not have to be your typical mahogany, maple, alder, ash, etc. There are a lot of different great woods out there to use, especially when building a steel because we don't have to worry about hanging 15 lbs off our neck all night. In the electric world, much of what is considered the typical "tonewoods" of today in reality was just what was easy to work with, economical, and available at the time. _________________ Some misc pics of my hand crafted steels
Follow me on Facebook here |
|
|
 |
Raymond Jones
From: British Columbia, Canada
|
Posted 27 Aug 2013 11:24 am Body resonance and vibrations -
|
|
Every material resonates and finds frequencies and vibrations that it is in tune with or not. The material can enhance (sympathies) or nullify these vibrations. This is the balance we go through to attain the sound we desire. Whether we build in wood,plastic, metals or even carbon fiber. I marvel at my Harmus, I feel the sound (by not having a body as such) allows the vibrations to form a flux of sound to surround the strings.
 |
|
|
 |
John RJ Wilson
From: United Kingdom
|
Posted 27 Aug 2013 1:45 pm
|
|
Stellar and informative responses chaps, which can be summed up by saying with regard to woods the same principles apply to lap steels as to standard electric guitars, no surprise there. What I cannot reconcile, and is probably my main reason for the post is that whilst the electric guitar has very few designs,in actuality, lapsteels appear to have a plethora of designs from ones carved out of one piece of wood to multipieced builds, ones designed for the lap, ones to lie on a table, ones for stands, which made me think, that a build can be any design as long as the scale length and certain principles were followed. Plus of course since I am a novice, and a geek I want to learn about the instrument as well as how to play it. _________________ Guyatone HG-91, Fender Hot Rod Deluxe, Ernie Ball Jr volume pedal. |
|
|
 |
David Matzenik
From: Cairns, on the Coral Sea
|
Posted 27 Aug 2013 2:17 pm
|
|
This subject has been discussed before, but I am not one of these people who think you have to dig up old posts just because you want to run some ideas past the gang. All the above points are valuable. But what is truly amazing is how the crappiest guitar can sound good. A friend came by with a piece of junk that I would not accept as a gift if offered, but when I plugged it in, it sounded pretty good. Some factor was working. It was not body material, tolerances, or workmanship. And the pickup probably cost ten bucks.
I have built my own steel guitar, and I put a lot of thought into tone and sustain, but this piece of crap broke all the rules.
One thing I believe was important in Rickenbacher alloy and Bakelite guitars was the integral bridge and nut. It allowed unrestricted transfer of vibration which must have a positive effect on sustain and body material induced tone. _________________ Don't go in the water after lunch. You'll get a cramp and drown. - Mother. |
|
|
 |
Tom Pettingill
From: California, USA (deceased)
|
Posted 28 Aug 2013 8:03 am
|
|
John RJ Wilson wrote: |
... which made me think, that a build can be any design as long as the scale length and certain principles were followed. ... |
Thats the core of it and one of the reasons I enjoy building my steels. Steel guitar has such a rich history to draw from and for myself, its a great creative outlet. Compared to "regular" electric guitars, there are less real, or perceived, design and construction restrictions. In our world of steel, you can go as simple as bolting some strings to a 2 x 4, or let yourself go and march to your own drummer.
Raymond Jones wrote: |
... I marvel at my Harmus, I feel the sound (by not having a body as such) allows the vibrations to form a flux of sound to surround the strings. |
The Harmus is a great example of thinking outside the box and doing it your way. Besides just being cool as hell looking, design wise I see some solid thought process behind it. The geometric structure is strong and rigid and the use of the end plates gives the strings a solid mounting point too.
David Matzenik wrote: |
... A friend came by with a piece of junk that I would not accept as a gift if offered, but when I plugged it in, it sounded pretty good. Some factor was working. It was not body material, tolerances, or workmanship. And the pickup probably cost ten bucks. ... |
Sometimes all the stars align and an outlier comes to the forefront. Was it an over the counter production model, or something home brewed. It would be interesting to see and know more about it and see what makes it tick.
Quote: |
One thing I believe was important in Rickenbacher alloy and Bakelite guitars was the integral bridge and nut. It allowed unrestricted transfer of vibration which must have a positive effect on sustain and body material induced tone. |
This touches on something to put in the maximize column. Regardless of design, solid coupling of the nut and bridge do make a positive difference. For example, I typically use a more "traditional" type nut and when I'm doing final assembly and tweaking the fine nut adjustments, I don't yet glue the nut down. Once I've got it dialed in, polished, and glued in place under string pressure, I can definitely hear a difference between un-glued and the next day after the glue has dried / cured.
Solid coupling is also the reason I do my set bridges the way I do. I do them much like acoustic builders do, mask the footprint and glue it down after finish. And because its a solid body, I can run my brass string hole liners long out of the backside to both further add coupling, forward shear resistance, and as a bonus they act as registering pins for precise location / relocation when its time to set it. The below pic might help to understand better what I'm talking about.
In the case of a screwed down metal bridge, if it came with screws, I toss them and replace with oversized and longer stainless steel screws. I use stainless because its stronger and the heads can be polished to high mirror shine. Longer because it gives you a better bite which means you can get it tighter and the longer metal screws have more potential transfer / interaction deeper into the body. Again, we are minimizing potential issues with the supplied weak and cheap pot metal screws and enhancing / maximizing our coupling.
.
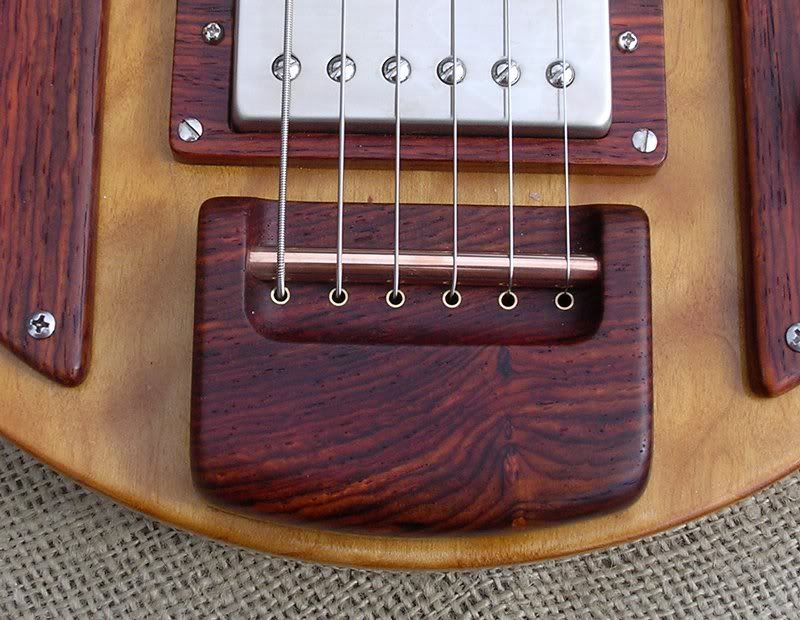 _________________ Some misc pics of my hand crafted steels
Follow me on Facebook here |
|
|
 |
Jim Pitman
From: Waterbury Ctr. VT 05677 USA
|
Posted 28 Aug 2013 2:22 pm
|
|
I built a nice lapsteel. Maple body capped with curly maple for the sound board and neck. I routed a cavity underneath the neck up into the sound board area. I regretted it. It resonates at about 600hz or so. Wound up stuffing it with foam to kill that resonance.
It sure does! |
|
|
 |
John RJ Wilson
From: United Kingdom
|
Posted 28 Aug 2013 3:14 pm
|
|
OK then i'll add in a couple more factors then since I've Opened (re-opended) the subject. Is there a finite difference between the effect on tone of a head stock back angled against just being straight off the neck? or is it just string mechanics and tuning stabilty?
Cylindrical bridges seem popular on Lapsteels, does this not make accurately measuring the scale length more difficult than neccessary as opposed to a simple right angled bridge, where the string break point will be more visually obvious. Or is the apex of the cylinder more forgiving tension wise, and thus less likely to be a string breaking point? _________________ Guyatone HG-91, Fender Hot Rod Deluxe, Ernie Ball Jr volume pedal. |
|
|
 |
Raymond Jones
From: British Columbia, Canada
|
Posted 28 Aug 2013 7:11 pm cylindrical bridge -
|
|
This goes directly with the fact that we use a cylindrical "steel" (of whatever material chosen)as the moving nut instead of pressing against a fixed fret. |
|
|
 |
Loyal McAvoy
From: California, USA
|
Posted 29 Aug 2013 12:02 am
|
|
The answer to your questions are; yes, no, no, yes, yes, no, sometimes, and maybe.
Sorry, couldn't resist; you bring so many issues to the table that each probably has a myriad of books written about each subject. I have found that a lot of your question's results are purely subjective, and depending upon which luthier you ask will yield a different answer. Practice and dedication always seem to trump all other considerations; that's why you can go on UTube and watch some guy play a guitar with his feet. |
|
|
 |
Tom Pettingill
From: California, USA (deceased)
|
Posted 29 Aug 2013 9:15 am
|
|
Loyal McAvoy wrote: |
The answer to your questions are; yes, no, no, yes, yes, no, sometimes, and maybe. ... |
LoL .. so true. While there is a consensus on many aspects of instrument building, there are just as many varying opinions too. My experience has been that if you toss out the extremes on both ends, that somewhere in the middle lies the truth. I certainly am no expert and I learn every day. My thought process has always been to try and learn why as opposed to how. And then, sometimes you just have to jump in and smash your thumb with a hammer to learn not to do that again
Quote: |
Is there a finite difference between the effect on tone of a head stock back angled against just being straight off the neck? |
Its all about getting sufficient down pressure across the nut. Too little and the strings will be floppy and tone can suffer. On the other extreme, at some point, more makes no difference. How you get there really does not matter.
Quote: |
Cylindrical bridges seem popular on Lapsteels, does this not make accurately measuring the scale length more difficult than neccessary as opposed to a simple right angled bridge |
At least for me, accuracy is not a problem, you simply measure to the center. I'd say to pick whatever style you feel comfortable with. If your worried about string breakage on a right angle setup, just slightly roll the back of the string slot when you cut it to avoid any sharp corners. _________________ Some misc pics of my hand crafted steels
Follow me on Facebook here |
|
|
 |
Andy Alford
|
Posted 29 Aug 2013 10:09 am Bobbe S.
|
|
You maybe able to find some post on tone that he did about 8 yrs. ago.He really made you think. |
|
|
 |
John RJ Wilson
From: United Kingdom
|
Posted 29 Aug 2013 2:43 pm
|
|
Sorry if I bring too many issues to the table, lifetime as a scientist I s'ppose, but when I get in to a subject I am like a sponge. I;ll try and limit my issues in future.  _________________ Guyatone HG-91, Fender Hot Rod Deluxe, Ernie Ball Jr volume pedal. |
|
|
 |
Brad Bechtel
From: San Francisco, CA
|
Posted 30 Aug 2013 6:24 am
|
|
John, please continue to bring as many issues to our collective table as you see fit. Don't let anybody scare you away from being a contributor to this forum. _________________ Brad’s Page of Steel
A web site devoted to acoustic & electric lap steel guitars |
|
|
 |