Author |
Topic: Quickest and proper way to restring a pedal steel |
Scott McRee
From: Georgia, USA
|
Posted 13 Jan 2016 8:40 am
|
|
Can someone post a video on they're technique of restringing they're steel? Thanks |
|
|
 |
Jack Stoner
From: Kansas City, MO
|
Posted 13 Jan 2016 10:11 am
|
|
No mystique to it. Remove all the strings, oil the nut rollers and wipe down the guitar, and then put the new strings on. |
|
|
 |
Tucker Jackson
From: Portland, Oregon, USA
|
Posted 13 Jan 2016 10:11 am
|
|
There's a link on the old Carter resource guide that had a slideshow on how to do a string change. Poke around on this site:
https://www.steelguitar.com/strings.html
Good luck. |
|
|
 |
Scott McRee
From: Georgia, USA
|
Posted 13 Jan 2016 10:34 am Thanks
|
|
Obviously I know you take the strings off. I'm asking y'alls technique. How not to scratch the lacquer. How to hold the string. Pre stretch or not etc |
|
|
 |
John Sluszny
From: Brussels, Belgium
|
Posted 13 Jan 2016 10:36 am
|
|
Yes,good luck !!! |
|
|
 |
Bo Borland
From: South Jersey -
|
Posted 13 Jan 2016 10:40 am
|
|
Tuckers' link above is great .. the only thing I didn't agree with was overlapping to line up the strings
Photo 11 is how they should look on the post , not the overlapped photo # 14
Depending on how YOUR machines line up with the roller nuts.. you may have to wrap to the outside instead of the inside |
|
|
 |
Scott McRee
From: Georgia, USA
|
Posted 13 Jan 2016 10:45 am Video
|
|
Anyone have any techniques that make it quicker? Also, anyone want to make a video and put it on YouTube? There is only one video. It's pathetic that we only have one video of restringing a stee. There is a million for other instruments |
|
|
 |
Allan Kelly
From: Watford, United Kingdom
|
|
|
 |
Patrick Laffrat
From: Gemenos, France
|
|
|
 |
David Nugent
From: Gum Spring, Va.
|
Posted 13 Jan 2016 12:17 pm
|
|
Scott...In the video, he is shown restringing a Magnum which features the slotted fingers. This method does not work as well if your guitar has the pins for holding the ball as it has a tendency to pop off the pin if constant pressure is not exerted. I normally measure and precut the string prior to beginning the process using the two tuner rule illustrated (for wound strings, 1 1/2 should be sufficient, otherwise there may not be ample space on the post). I first attach the string to the tuner post, make one turn to hold it in place, then gently bend the ball end around the tip of my finger to facillitate attaching the ball to the pin (or slot). FWIW: I find it easier when changing the entire set to install strings one through five, and then ten through six in that order. Working the final five strings toward me while leaving the space open between seems to leave more room for my rather large fingers to work. |
|
|
 |
John McClung
From: Olympia WA, USA
|
Posted 13 Jan 2016 1:46 pm
|
|
Scott, that Carter video by John Fabian is poor in image quality, and that method of how to measure and cut the string to the proper length was a bit murky to me, but it's something I'll try to master someday.
And to protect the tuning keys cavity lacquer, get some thin vinyl or plexiglass (clear or any color you like), measure and cut to shape and put it in there to protect your Williams' finish. _________________ E9 INSTRUCTION
▪️ If you want to have an ongoing discussion, please email me, don't use the Forum messaging which I detest! steelguitarlessons@earthlink.net |
|
|
 |
Scott McRee
From: Georgia, USA
|
Posted 13 Jan 2016 2:16 pm For sure
|
|
Yea I already have the thin plexi. I need to cut it still. I'm waiting the arrival of my baby Williams tonight by 6:00. So fu***&;-&/$ing pumped haha |
|
|
 |
John Sluszny
From: Brussels, Belgium
|
Posted 13 Jan 2016 4:19 pm
|
|
John McClung wrote: |
And to protect the tuning keys cavity lacquer, get some thin vinyl or plexiglass (clear or any color you like), measure and cut to shape and put it in there to protect your Williams' finish. |
Great and fantastic idea ! Thank you John ! |
|
|
 |
Ian Rae
From: Redditch, England
|
Posted 13 Jan 2016 4:41 pm
|
|
Patrick Laffrat wrote: |
it is not absolutely necessary to sing during the operation |
I'm glad - that's the part I was finding tough _________________ Make sleeping dogs tell the truth!
Homebuilt keyless U12 7x5, Excel keyless U12 8x8, Williams keyless U12 7x8, Telonics rack and 15" cabs |
|
|
 |
Jeff Mead
From: London, England
|
|
|
 |
Ian Worley
From: Sacramento, CA
|
Posted 13 Jan 2016 6:16 pm
|
|
That's great Jeff! Good thing he broke it on a song in E, he even got his ride in there |
|
|
 |
Tom Quinn
|
Posted 14 Jan 2016 5:04 am
|
|
Jack Stoner wrote: |
No mystique to it. Remove all the strings, oil the nut rollers and wipe down the guitar, and then put the new strings on. |
Wise guy... _________________ I need an Emmons! |
|
|
 |
Bill Moore
From: Manchester, Michigan
|
Posted 14 Jan 2016 5:53 am
|
|
Changing strings is something that gets easier the more you do it. I think it's best to take your time at first, you don't need to change all 10 strings at once, just do a couple at a time. Make sure the plain strings have a good number or wraps on the tuner, and try to wind them so they are well aligned with the roller. Don't wind a full length string, cut it to the right length before winding. And bend the end with pliers, make it short so it won't scratch up the finish as it turns. Just take your time and pay attention to what you are doing, it will get easier. |
|
|
 |
Bob Hoffnar
From: Austin, Tx
|
Posted 14 Jan 2016 6:29 am Re: Video
|
|
Scott McRee wrote: |
Anyone have any techniques that make it quicker? Also, anyone want to make a video and put it on YouTube? There is only one video. It's pathetic that we only have one video of restringing a stee. There is a million for other instruments |
I use a string winder that connects to a power drill. Speeds it up quite a bit. Also I see no reason to add plastic to the head stock. All you need to do is not push the string to far through the tuning key.
I take all the strings off so I can clean up my steel easily. Although if you change one at a time you will have a handy visual reference of what direction the string goes.
If your steel has pins holding the string instead of a slot in the bridge stick something handy in there to hold the string on while you tighten it.
After doing it a couple times you will see how simple it is and why there is no need for a video. If you are into videos you could make an in depth study of the million videos of guitar players changing there strings then apply those principals to your steel. After you have mastered string changing you could make the ultimate video for us. _________________ Bob |
|
|
 |
Jim Pitman
From: Waterbury Ctr. VT 05677 USA
|
Posted 14 Jan 2016 12:12 pm
|
|
I like to use a wooden wedge cut from 3/8" thick hardwood flat stock to trap the ball end of the string at the changer. My wedge is made from oak. It's about 2" long and pointy at one end while the other end is about 3/8" across. (square in cross section at this end). I could envision one made from hard rubber.
I push it in, pointy end down, behind the current finger and the neck end piece, in that cavity that always exist in every PSG. Trapping that end means you can use both hands on the key head end of the string without worring about the changer end coming off.
I use one of my manual (cordless/battery-less) string winders to speed up the key head end. It's fast, never fails, and never runs out of juice. |
|
|
 |
Jeff Mead
From: London, England
|
Posted 14 Jan 2016 12:25 pm
|
|
Jim Pitman wrote: |
I like to use a wooden wedge cut from 3/8" thick hardwood flat stock to trap the ball end of the string at the changer. My wedge is made from oak. It's about 2" long and pointy at one end while the other end is about 3/8" across. (square in cross section at this end). I could envision one made from hard rubber. |
I use a rubber wedge like this. They are sold as a tool that piano tuners use. They are called Piano Tuning Mutes or Mute Keys. |
|
|
 |
Steve Vroman
From: Albany, NY
|
Posted 15 Jan 2016 11:51 am
|
|
Just completed my first string change on my Stage 1. I was kind of nervous but I just worked slowly and changed one string at a time. Could be a little straighter off the roller but I'm pleased overall. I went with LiveSteel strings and pretty much stuck with the same gauges as Doug set it up. I did bump up the third string to a .0115 and that seems to work for me. My initial impression of these strings is great, maybe a little more girth than the GHS. I really like how the sound decays too, if that's the right word for it
Much thanks to Doug for building me such a nice guitar and to the forum for all the good info. I've only been playing about six months but it's been great fun
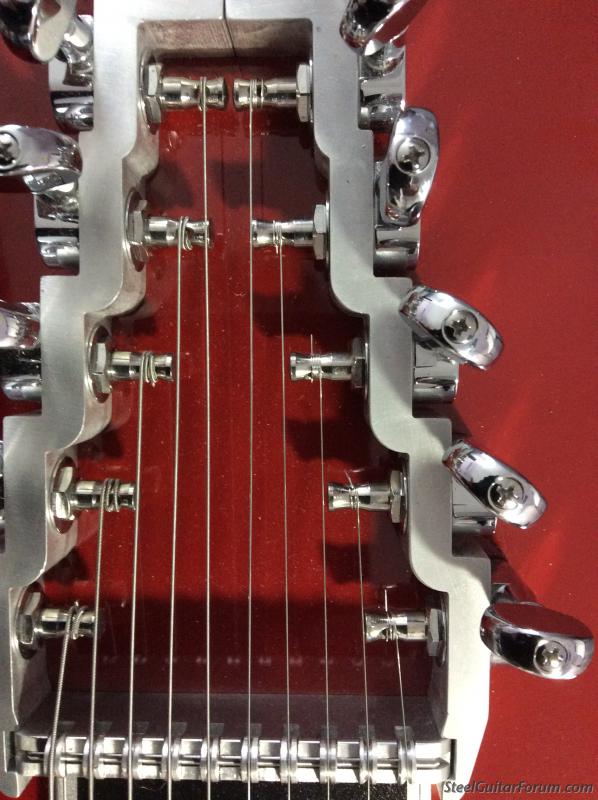 |
|
|
 |
Ian Rae
From: Redditch, England
|
Posted 15 Jan 2016 12:03 pm
|
|
Steve, that's a tidy job but I wonder how many folk would prefer to see more turns round the posts, especially on the plain strings. I put at least half a dozen. I may be paranoid, but I've never had one break that end. _________________ Make sleeping dogs tell the truth!
Homebuilt keyless U12 7x5, Excel keyless U12 8x8, Williams keyless U12 7x8, Telonics rack and 15" cabs |
|
|
 |
Tucker Jackson
From: Portland, Oregon, USA
|
Posted 15 Jan 2016 12:08 pm
|
|
Ian, you just beat me to it.
Steve, you did a nice clean job. You might want to cut those strings just slightly longer before installing next time. What you have should work OK for now, but that sixth string is over the hole -- meaning it might take some unnecessary wear if there is a burr around the lip of the hole. On thinner strings especially, this can sometimes be the cause of breakage at the keyhead end.
Also, as Ian pointed out, the thinner strings want more turns than the thicker ones. The first string is probably OK, but you might have slippage if you use the raise lever a lot. Probably not, but a couple more wraps next time will remove all doubt. You're good for now -- nice and straight over the roller nut...now go play that awesome guitar!
Last edited by Tucker Jackson on 15 Jan 2016 12:15 pm; edited 1 time in total |
|
|
 |
Steve Vroman
From: Albany, NY
|
Posted 15 Jan 2016 12:13 pm
|
|
I was wondering about the number of turns. As far as string length, I did 1 and 1/2 past the post for the wound, two for the plain, and four for the g#. The original set of strings did have more winds. Good thing I bought extra strings ! |
|
|
 |